ツマミのお話 あれこれ -2
※ 先に前記事『ツマミのお話 あれこれ -1』をご覧になるにはこちらをクリックください。
ツマミの本体材料は、どのような物なのでしょう?
少ない部品点数にてシンプルに構成されているツマミですが、少し掘り下げて各部分のキャラクターを見てみましょう。
◎ 本体の主材料
【樹脂】と【金属】の二種類とは?
● 【樹脂】 = モールド (プラスチック製) → 熱硬化性樹脂=フェノール樹脂 or 熱可塑性樹脂=ナイロン樹脂、ABS樹脂 など
● 【金属】 = メタル(金属製)=アルミニウム + アルマイト処理 ということになります。
◎ 各主材料の特徴
● モールド → K-1、K-300、K-2195など 大きく分けて、熱硬化性と熱可塑性の樹脂があります。
熱硬化性の樹脂は、固体の材料に熱を加えて溶融させ、金型内に作られた空間に射出し、さらに熱を加えると化学反応により固まる(硬化させる)ものです。 この方法は射出成型といわれる成型方法ですが、金型内に粉末や粒状の材料を入れたのちに、加熱し金型ごとプレスする方式の「圧縮成型」というやり方もあります。
☆ミニミニ知識: 射出成型は、インジェクション成型、圧縮成型は、コンプレッション成型とも呼ばれています。
(圧縮成型は、材料が少なすぎると、成型品の形状において欠けが出てしまったり、スカスカになったりして樹脂としての性能が出ません。 また、多すぎると全てバリとなってしまうので、後処理(バリ取り)が大変になるばかりか寸法も出ませんので、しっかりと計量したものを金型に入れます。)
射出成型は、人が眠りについて夢を見ている頃にもせっせと機械が仕事をしていてくれますが、圧縮成型は自動化が困難なので、特別な場合を除き、今ではあまり見かけなくなっています。 しかし、圧縮成型ならではの高密度の成型品が得られたり、成型時の材料の流れの方向性が少なく、比較的反りが少ないなどの有益な要素を持った、歴史のある成型方法でもあります。
通常あまり必要はないかとは思いますが、射出成型で作られたのか、圧縮成型で作られたものなのかを成型された現物で見分けることができます。 射出成型では、金型内に製品の形をした空間があり、そこに溶融した樹脂材料を射出(注入)するための「ゲート」という注入口があり、成型品にはその跡(ミリ単位の円形や長方形など)が残ります。 圧縮成型では、ゲート自体がありませんのでそのような跡がありませんから容易に判別が可能です。(射出成型と圧縮成型の中間?のようなトランスファー成型という方法もありますがここでは触れないことにします。) なお、熱硬化性の樹脂は、不可逆的な性質を持っており硬化後は熱を加えても再び融けることはありません。 --- 代表的なものに、フェノール樹脂があります。 K-1、 K-2195など。
一方、熱可塑性の樹脂は、固体(その多くはペレット状)の原材料に熱を加えて溶融させ、金型内の空間に射出し冷却することで固化させて成型品とします(射出成型)。 成型品を再加熱すると溶融し、可逆的であるため比較的容易にリサイクルすることも可能な樹脂です。 ただし、再度成型を行うごとに少しづつ物性の劣化があるので、適切な管理が必須となります。 --- ナイロンやABSなどがあてはまります。 製品では、K-200、 K-300など。
オフィスのように樹脂にとって恵まれた環境で使用される事務機器等であれば、材質について意識せずともほぼ問題はありませんが、使用環境によってはその適性を確認したうえで使用するのが好ましいといえます。
この二種類の成型材料の性質上、熱硬化性樹脂の成型金型は「熱く」、熱可塑性樹脂の成型金型は「冷たい」ということになります。
とはいえ、あくまでも二つの温度を相対的に比較した結果であって、冷たいとは言っても、人の感覚で言えば「熱い」です。 なお、熱硬化性樹脂の成型金型は一般にヒーター等を使用して加熱し、手で触れば即火傷するような温度です。 熱可塑性樹脂の成型金型は、溶融樹脂の注入によって徐々に温度が上がっていってしまいますが、金型内に水や油を通して冷却し、温度調節器にてコントロールされています。 冷却とはいえその温度は、体温より高いことが多いので「熱い」ということにはなります。(その温度は少なくとも数十℃程度以上であることが多いです。)
射出成型であれ、圧縮成型であれ、成型品を金型から取り出すたびに、金型を開いて2つまたは3つに分割します。 そして、パーティングライン(Parting Line、PL)と呼ばれる金型が分かれるラインがあり、金型から取り出された成型品には必ず小さなパーティングラインが残ります。 通常、そのラインから樹脂がはみだして、「バリ」と呼ばれるものが出来てしまいますが、これをできるだけ小さくすることで、成型後の「後処理」の手間を省くようにします。 しかし、なんといってもバリを出さないことが外観上もきれいであるため、金型精度の向上や成型条件の調整等生産現場では毎日が戦いとなっています。
☆ミニミニ知識: ちなみに、圧縮成型は俗に「バリを出させて成型する」方法とも言われており、バリの後処理が結構大変です。
☆ミニミニ知識: 射出成型の成型品取り出し後の金型は、成型機によって自動的に閉じられますが、次の溶融樹脂の射出(材料注入)の圧力によって、金型が開いて隙間ができてしまうとバリ発生の原因になりますのでとても強力に締付けます。 型締力(かたじめりょく)と呼ばれるその値は、例えば100tfなどと、とても大きなものです。(100tf = 100トンの力)
***** どうでもよい、筆者のこだわり *****
ここまでに、何度も「せいけい」という言葉が出てきましたが、漢字で書いた時の「せいけい」に、ちょっとした こだわりを持っています。 「せいけい」は、(あるもの)を(かたちづくる)ことと思っています。
いろんなシーンで使われている漢字を見ますと、「成形」と「成型」がほぼ同じように使われています。
ここで、筆者のこだわりは、「成形」は、文字通り形を成すことであり、「成型」は、「型」を使って「形」を「成す」ということです。 ということで、どちらの漢字を使っても間違いではないと思うのですが、弊社のようなものについては型を使用して形作っているので「成型」が、より的確なのではないかと、、、思うのです。(実際、この考えが正しいのかどうかは調べていませんので不明です。 ただ単に癖の強いこだわりかもしれません。) ちなみに、「整形」は「形」を「整える」ことを言うのでしょうね。
さてさて、だいぶ寄り道をしてしまいましたが、本流に戻りたいと思います。
● メタル → K-29、K-59など アルミニウムにアルマイト処理を施しています。 市場にはモールドに薄いアルミを被せたり貼り付けたりして作られているツマミが多い中で、弊社のメタルツマミは、全ての製品でアキラ100%ならぬアルミ100%と、最強です。 安心してください、アルミ無垢ですよ!ということになります。 どなたです? 無垢は、アルミではなく金がいいなんて言っているのは。 そりゃー、筆者だってそうですけど、、、、、。 金無垢のツマミ、一個100万円ではちょっと、、、 そういえば、だいぶ前どこかに、純金風呂なんていうのがありましたが、、、、、
メタルツマミの特長は、重量感と超高級感ですが、重量感については「重い」ということにもなりますので、場合によっては重量感とは裏腹に使用の機器が多少重くなるといった短所にもなりえます。 また、超高級感は無垢のアルミ材からの削り出し(切削加工)によってもたらされるものであるため、コストがかかってしまうのもまた短所といえばそうなりますね。
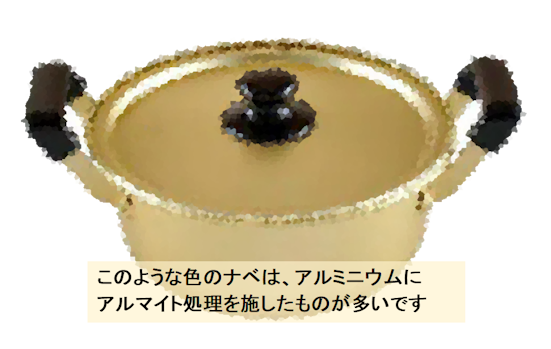
身近なナベもアルマイト処理
ここで、アルマイト処理について、ごく簡単にご紹介します。 アルマイトは、陽極酸化処理とも言われ、アルミニウム(被処理物=ツマミ本体)を陽極(+極)に置き、電解処理によって表面に人工的に酸化皮膜を生成させる表面処理のことです。 普通のめっき処理ですと、表面を例えばニッケルや金などの薄い層で覆うのですが、その層の部分の金属を、自らのアルミの酸化被膜としたものと考えれば分かりやすいかと思います。 目的は、耐食性、耐摩耗性、美観性の向上などがあげられます。 表面は、いわゆるアルミ色だけでなくいろいろな着色も可能です。 アルマイト処理というと、身近なところでは、アルミサッシの表面、黄色っぽい色のアルミナベの表面処理などにも使われています。(ナベの色のツマミは弊社にはございません)
最後に、一般のツマミと、ナベのツマミ(とって)ってよくよく見比べると似ているものありますね! そのようなツマミのことを、【ナベブタツマミ】と呼んでいた人がいたのを覚えています。
一部、UFO型ツマミと呼ばれていたものもありました。 そう言われてみると、なにかそんな形に見えてきませんか?
指示線や指示点など(取付面に表示された目盛などを指示する目的で設けられた線や点等)
● なし → どのくらいツマミが回転したかを示す必要がない用途向けです。
● あり(線、点、三角形、数字) → ツマミがどれだけ回転したかを視覚上確認する必要のある用途向けで、ツマミの円周上に何らかの目印を付けております。 切削や金型(成型)などで形成された溝部や凹部にペイントを充填したり、印刷や樹脂製の指示線ピース装着などにより設けられます。それぞれの例をあげますと次のようになります。
1. なし → K-220
2. 線 → K-1-A、K-90、K-100
3. 点 → K-6、K-29、K-8075
4. 三角形 → K-75
5. 数字 → K-1-B
6. 溝のみ → K-32
7. 指示線ピース装着 → K-210
取付け(締め付け)用のねじ
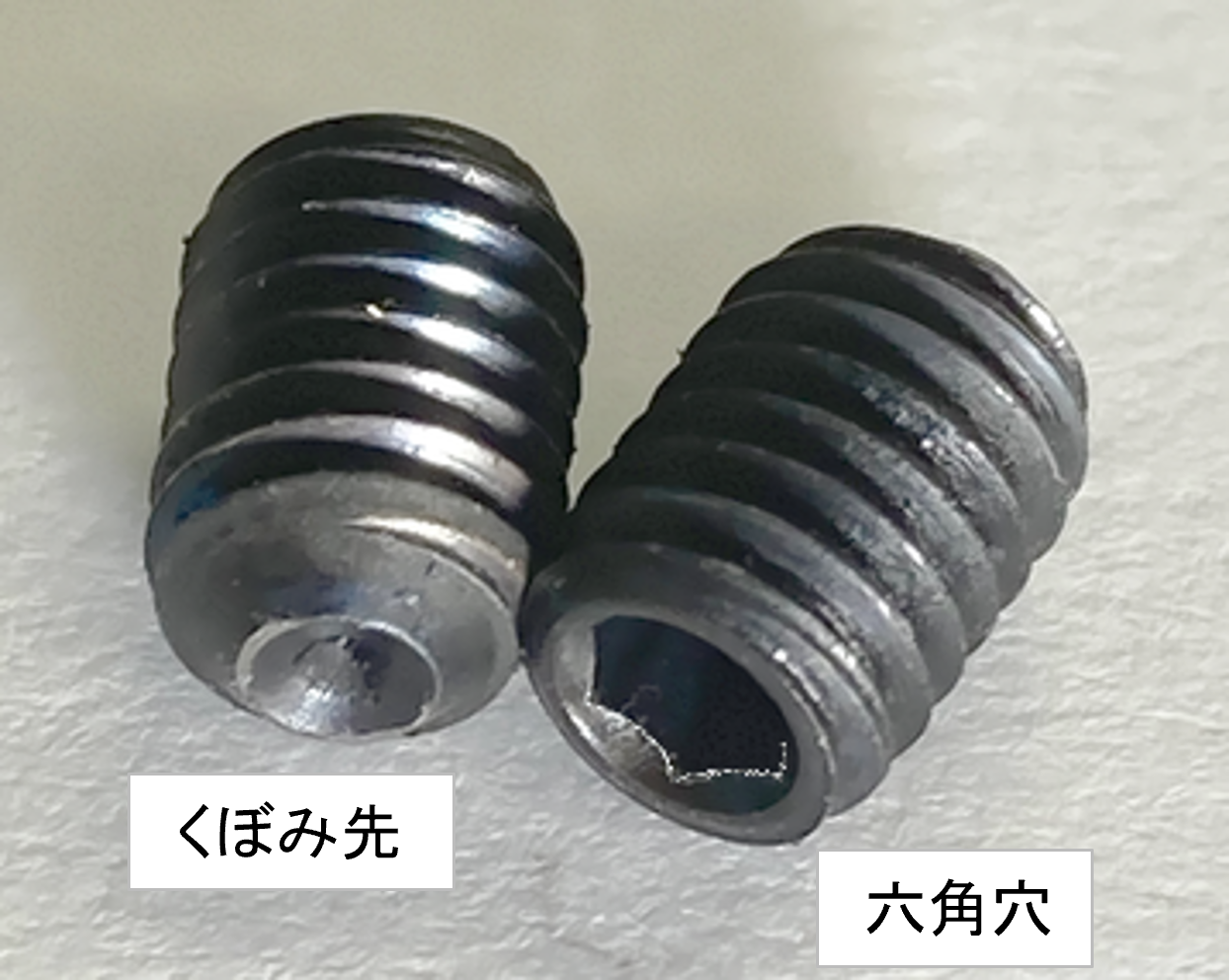
六角穴付きねじ
ねじによってツマミを固定しますが、ねじには一般に次の2種類が使われています。
● 六角穴付きねじ → 頭部に六角形の凹部があり、六角レンチ(工具)に対応したもの。 弊社で使用しているものは先端がカルデラ状に窪んでいて、「くぼみ先」と呼ばれており、平面に締付けた場合、円形の締付け跡がつきますが、円柱状のシャフトの場合は、「こ」の字形に跡がつきます。 比較的強固に固定でき、かつ、相手を傷付けにくく、一度外したあとに再度取り付けることが可能で、バランスが良いのが特徴です。 (現在、弊社製のほとんど全てのツマミにはこれが使用されています。)
● すり割り付きねじ(マイナス) → 頭部に溝があり普通のマイナスドライバー用のもので、旧来より多用されてきたねじです。
取付け(締め付け)の方法
ねじによってツマミを固定しますが、その方式には次の2種類があります。
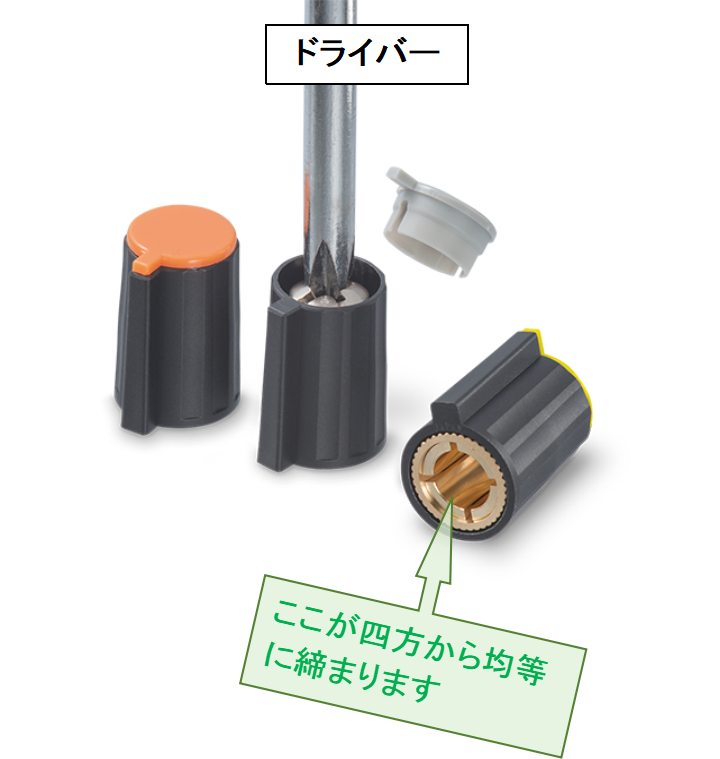
コレットチャック式
● ボリューム等のシャフトの長手方向に対して90°横方向から、ねじを締めることによって、ねじの先端をシャフトに押し付けてツマミを固定する方法(仮に、横ねじ締め付け式 と呼ぶことにします)----- 既出。 『ツマミのお話 あれこれ -1』内のイラストのもの
● ボリューム等のシャフトの先端の方向にセットされたねじを締めることによって、ツマミ内部の部品がシャフトの円柱部の周りから締付ける方法(コレットチャック式)----- 左図のもの
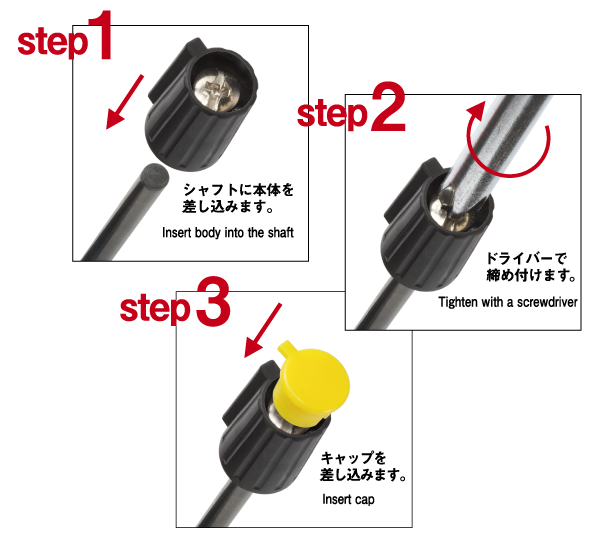
コレットチャック式は3stepで
コレットチャック式のツマミは、3 step. 左図のようにシャフトに上からツマミを被せて、ヌートバー?ではなくてプラスドライバーでねじを締めます。 そして、ねじを隠すキャップをはめ込めば完了です。 使用されているねじは、プラス、マイナス両用の ”プラマイ” ですが、マイナスドライバーですと横に滑りやすいことに加えて、センタリングされにくいことによりツマミ内部を傷付けてしまうこともあるため、仕様上、プラスドライバーを推奨しております。
各締め付け方法の特徴
● 横ねじ締め付け式
ツマミによって異なりますが、1本または2本のねじでボリューム等のシャフトの横方向から締めますので、シャフトの径とツマミのシャフト収容部の径の差によって若干ではありますが、シャフトがねじの反対側に押され、収容部の中心からずれが生じます。 イラストをご参照ください。
一例をあげますと、計算上0.05mmほどの心ずれが生じます。これに、ツマミとシャフトの公差を考慮した場合、ずれは0.025~0.125mmの範囲となります。 ねじの締付を横方向から行うため、狭い範囲に複数のツマミを密集して設置する場合や、他の部品等がある場合は、使用する工具にもよりますが、ねじ締め作業が難しいことがあります。 構造がシンプルであることや、コスト的に有利であるため、ほとんどの製品にて採用されている方式です。 なお、ねじは先述の、先端形状が、「くぼみ先」と呼ばれる形をもった鋼でできており、シャフトに程よく食い込む(食いつく)ようになっていて滑りにくくなっております。
● コレットチャック式
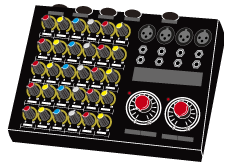
密集取付の例
横ねじ締付け式とは異なり、ツマミの上部(シャフトの先端方向)からプラスドライバーで締める方式です。これは、ドリルの刃や工具類を取り付ける方法と同じもので、シャフトの円柱を周りから絞って、口をすぼめるような形で咥える(くわえる)ので、自動的にシャフトはツマミの真ん中に「センタリング」されますので、仕組み的に実用上の、ずれ(偏心、偏芯)は起こりません。
特長は、上記のように心(芯)ずれの心配がないこと、シャフトにキズを付けにくいこと、普通にどこにでもあるドライバーで取付けができ、ねじの締付け作業が格段にやりやすいこと、取り付け後に取付け用のねじが見えなくなることなどがあげられます。 例えば音響用ミキサーのように密集して取付ける際に、横からねじを締める方式だと、工具が入りにくく作業に困難を伴うことがありますが、普通のドライバーでツマミの上側から締めることができるコレットチャック式なら、楽々作業ができます。 短所としてはほぼ一点。 部品数が増え、加工工程が異なるため生産コストのアップがあげられます。 この特長とコストを天秤にかけて、どう考えるかが使用のカギとなると思われます。
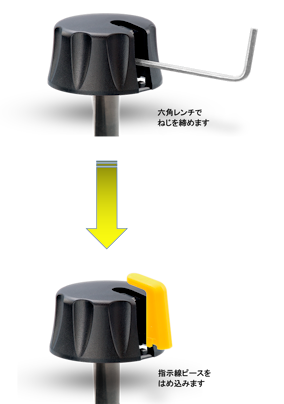
指示線ピースを嵌めればねじの穴が見えなくなります
ねじが見えなくなるということでいえば、ちょっと変わったところで横ねじ締付け式であっても、K-210があります。 これは、横ねじ締め付け式なのですが、ねじ締め付け後に、そのねじ穴部分に指示線となる樹脂のピースをフタのように被せることで実現しています。
一般に、横ねじ締め付け式の場合は、ツマミの横にねじの穴があり、横方向からみるとそれが見えてしまうのでますが、その穴を含む特定の範囲を樹脂製のピースで覆い、穴を隠したうえで、その樹脂ピース自体を指示線としてしまうことでさりげなく目的を達成しています。
ツマミは造りが単純であり、なにも考えるようなことはないものと思いきや、たかがツマミ、されどツマミで、掘り下げていくと意外といろいろなことが出てきます。 製造する者から見たツマミ、使用されるお客様から見たツマミなど、見方によっても異なることも多々あるものと思われます。 書ききれなかったことが、まだたくさんあるのですが、このへんで筆を置きたいと思います。
今回も、最後までお読みくださりありがとうございました。
※ ふたたび、前記事『ツマミのお話 あれこれ -1』をご覧になるにはこちらをクリックください。